How AI is Solving Supply Chain Chaos
The days of clipboards and gut instincts are over—see how smart companies are revolutionizing their supply chains with automation that actually works.
In a warehouse outside Seattle, a robot glides silently between towering shelves. It stops, extends its mechanical arm, and precisely selects a package. No human directed it. No one programmed this specific movement. The robot decided—based on complex algorithms—which item to pick next. This isn't science fiction. This is supply chain automation today.
Supply chains were once defined by clipboards, phone calls, and gut instincts. Now they're driven by artificial intelligence, machine learning, and autonomous systems that make decisions faster than any human could. The transformation isn't just changing how goods move from manufacturer to consumer—it's fundamentally altering the competitive landscape of global business.
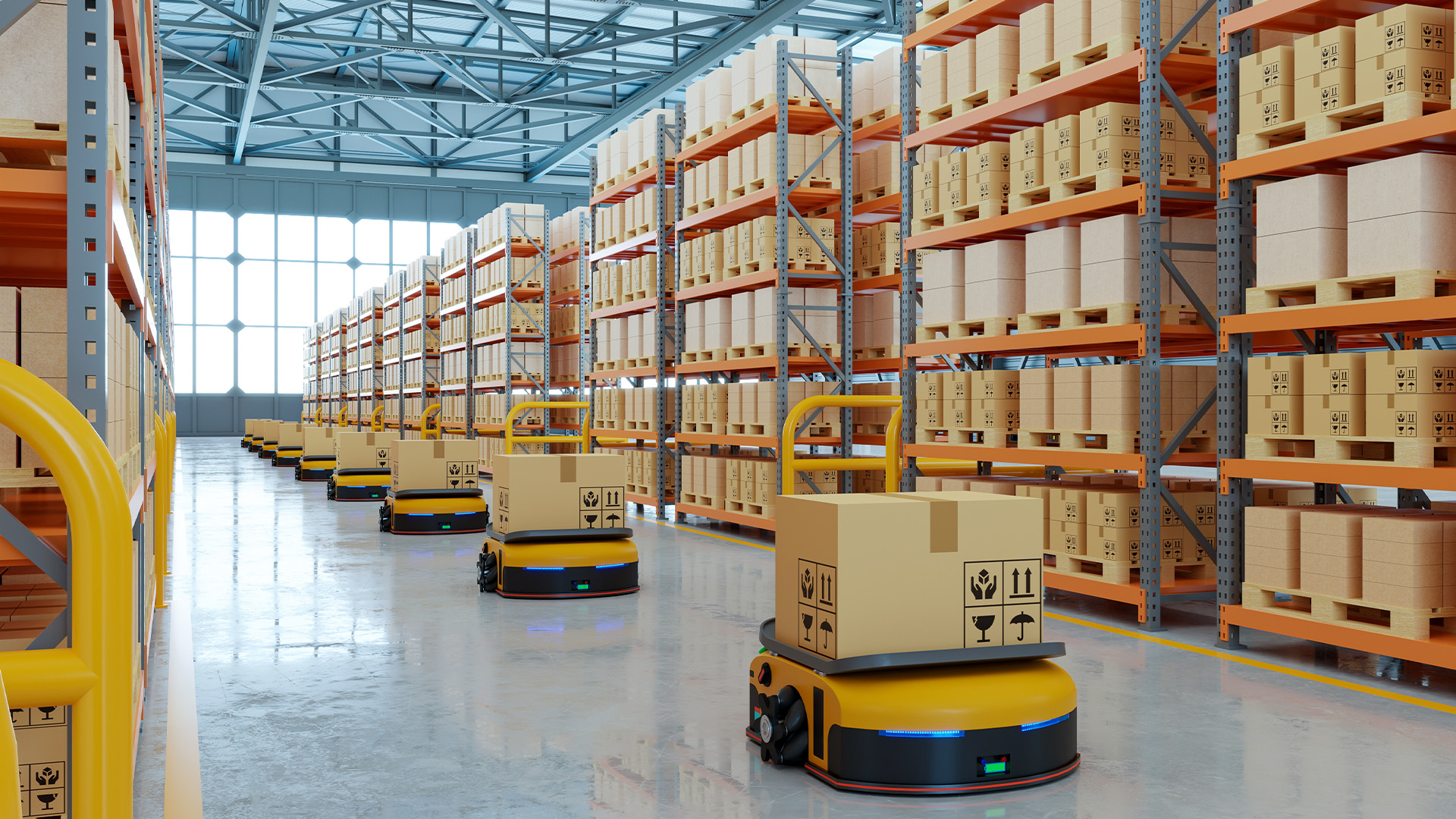
For companies that embrace this revolution, the rewards are substantial: reduced costs, increased efficiency, improved accuracy, and enhanced customer satisfaction. For those that don't, the future looks increasingly uncertain. The gap between automated supply chains and traditional ones widens every day, creating a competitive divide that will be difficult to cross once established.
This isn't just about robots in warehouses. It's about intelligent systems that predict demand before it happens, software that reroutes shipments around problems before they cause delays, and analytics that spot inefficiencies invisible to the human eye. Supply chain automation represents perhaps the most significant operational transformation since the assembly line—and we're just getting started.

The Evolution of Supply Chain Management
Supply chain management has undergone a remarkable transformation over the decades. What began as simple logistics—moving products from point A to point B—has evolved into a sophisticated ecosystem of interconnected processes, technologies, and strategies. The journey from manual operations to automated systems tells a story of innovation driven by necessity.
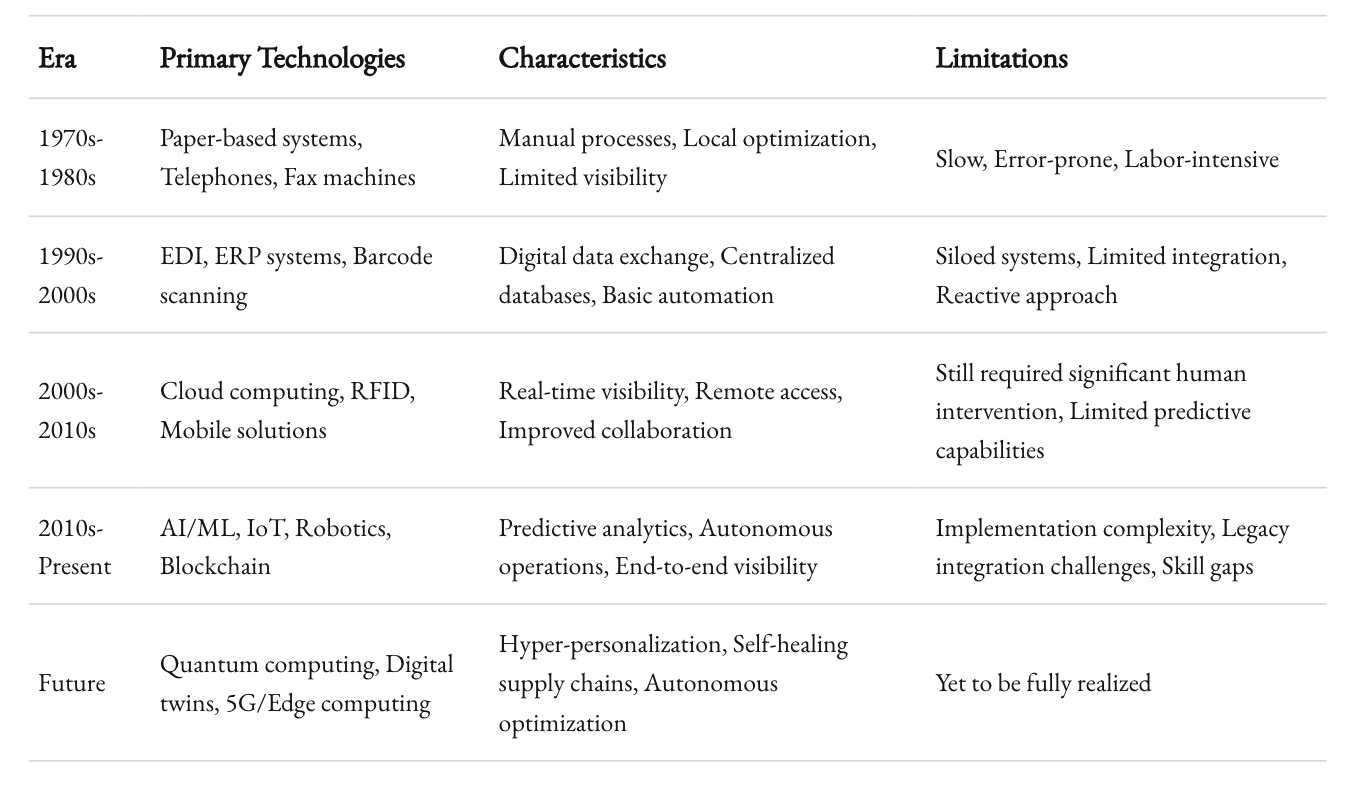
In the 1980s and early 1990s, supply chains operated primarily through manual processes. Orders were placed by phone or fax. Inventory was tracked on paper. Shipping routes were planned using physical maps and local knowledge. The system worked, but it was slow, error-prone, and resistant to scaling. As businesses expanded globally, these limitations became increasingly problematic.
The introduction of Enterprise Resource Planning (ERP) systems in the late 1990s marked the first significant step toward digitization. These systems centralized data and provided visibility across different functions, but they still required substantial human intervention. The real breakthrough came with the internet revolution, which enabled real-time communication and data sharing across global supply networks.

Today's supply chains bear little resemblance to their predecessors. Modern systems leverage artificial intelligence, Internet of Things (IoT) sensors, blockchain, and advanced analytics to create intelligent networks that can sense, respond, and adapt with minimal human intervention. This evolution hasn't been linear—it's accelerated dramatically in recent years, driven by technological advances and competitive pressures that make automation not just advantageous but essential.
The Technology Driving Modern Supply Chain Automation
The technological foundation of supply chain automation consists of several interconnected innovations that work together to create intelligent, responsive systems. Understanding these technologies is crucial for companies looking to implement effective automation strategies.
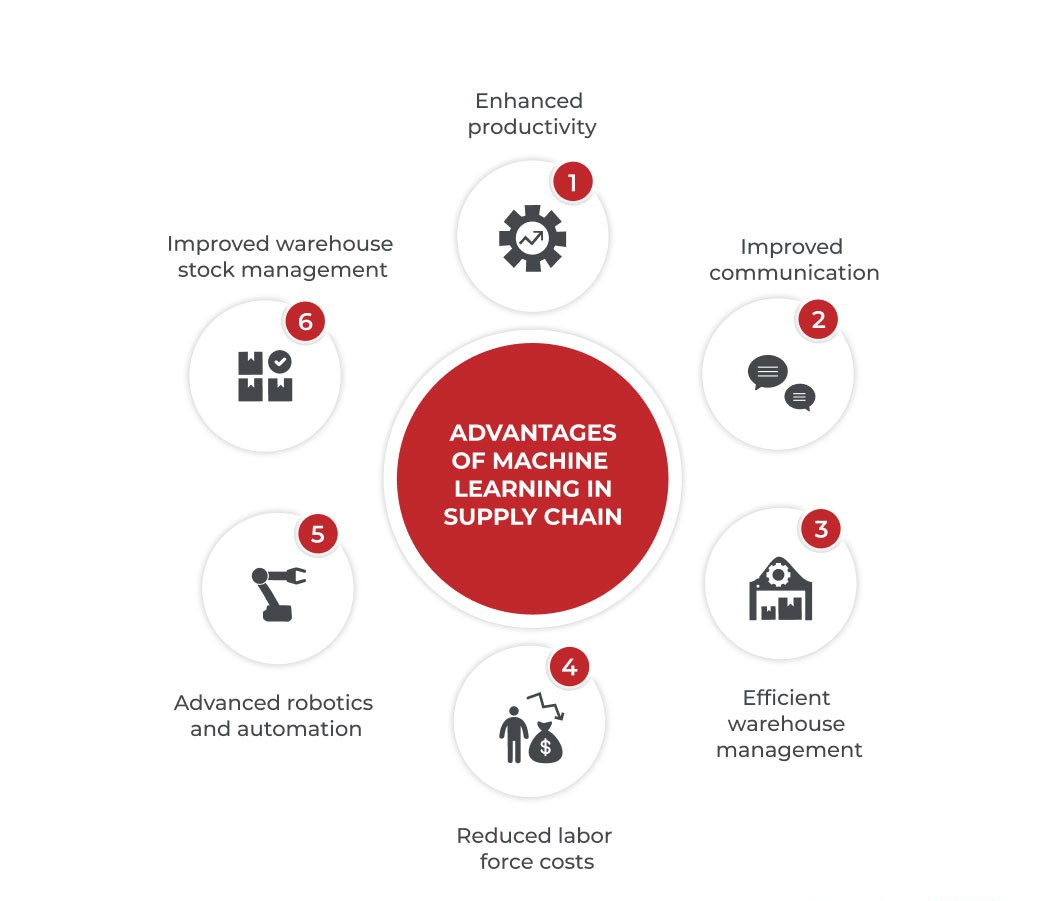
Artificial Intelligence and Machine Learning stand at the forefront of supply chain transformation. These technologies enable systems to analyze vast amounts of data, identify patterns, and make predictions with remarkable accuracy. In demand forecasting, AI algorithms can consider hundreds of variables—from historical sales data to weather patterns to social media trends—to predict future demand with precision that human analysts simply cannot match. This predictive capability reduces inventory costs while ensuring products are available when and where customers want them.
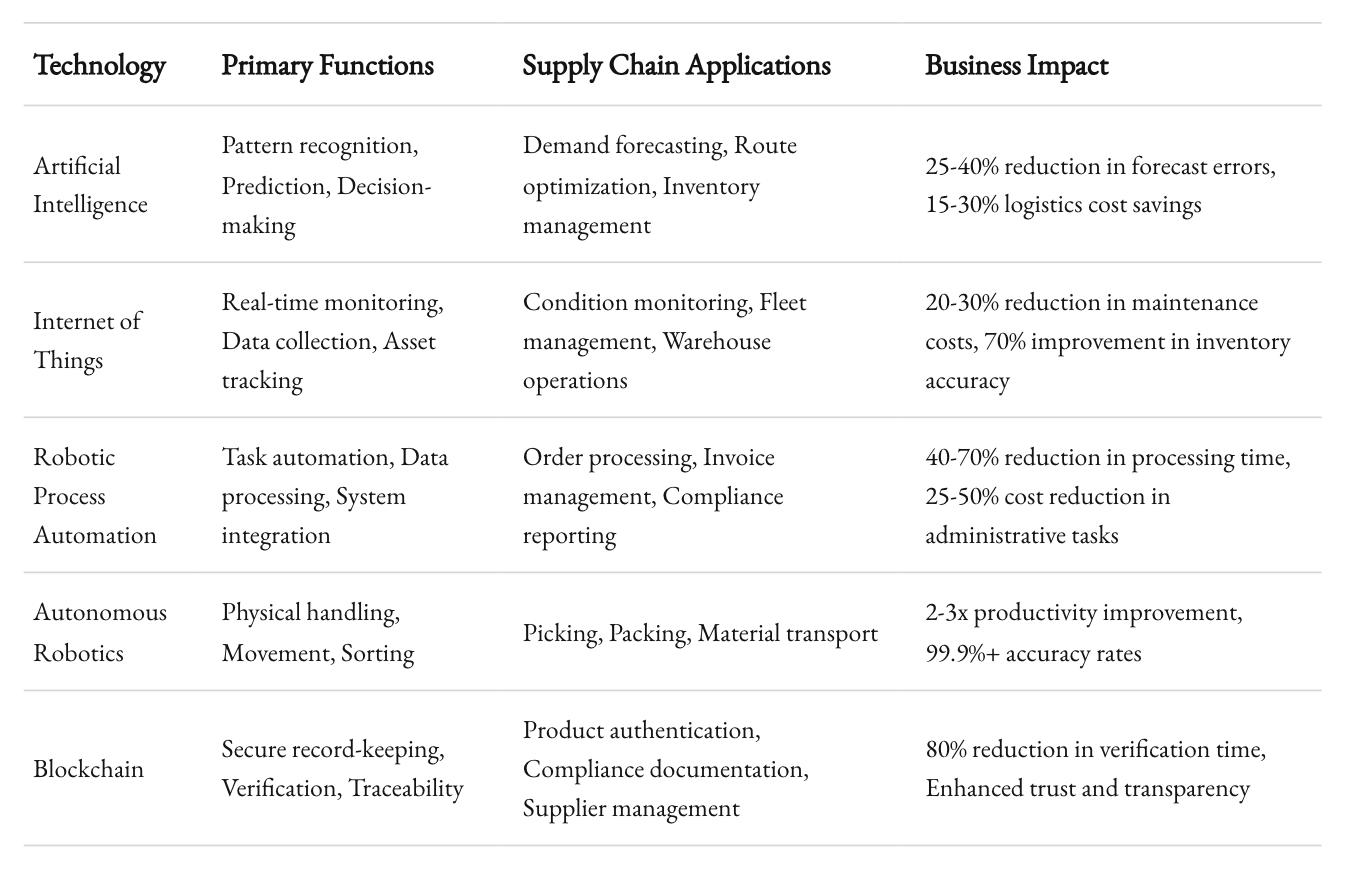
The Internet of Things (IoT) provides the sensory network that feeds data to AI systems. Smart sensors attached to products, vehicles, and equipment transmit real-time information about location, condition, and environment. A shipping container crossing the Pacific can now report its exact location, internal temperature, humidity levels, and whether it's been opened or tampered with. This continuous stream of data enables visibility and control that was unimaginable just a decade ago.
Robotic Process Automation (RPA) handles the repetitive, rule-based tasks that once consumed countless human work hours. From processing purchase orders to managing invoices to updating inventory records, RPA bots work tirelessly, consistently, and without error. They free human workers from mundane tasks while reducing processing times from days to minutes or seconds.

Autonomous vehicles and robotics are perhaps the most visible aspects of supply chain automation. Automated guided vehicles (AGVs) navigate warehouse floors, retrieving and delivering items without human guidance. Robotic arms pick, pack, and sort with precision and speed. Drones inspect inventory in high shelves or deliver packages to remote locations. These physical automation systems work around the clock, don't require breaks, and perform consistently in environments that might be dangerous or uncomfortable for human workers.
Blockchain technology is emerging as a powerful tool for supply chain transparency and security. By creating immutable records of transactions and movements, blockchain enables trustworthy tracking of products from raw materials to finished goods. This capability is particularly valuable in industries where authenticity and provenance matter—pharmaceuticals, luxury goods, and food safety, for example.

Real-World Applications Transforming Industries
The impact of supply chain automation varies significantly across industries, with each sector finding unique applications that address its specific challenges and opportunities. These real-world implementations demonstrate the versatility and power of automation technologies.
In retail, automation has revolutionized inventory management and fulfillment. Amazon's fulfillment centers represent perhaps the most advanced example, with robots and humans working in orchestrated harmony to process millions of orders daily. The company's automated systems determine optimal storage locations for products based on demand patterns, guide robots to retrieve items efficiently, and even predict which products customers will order before they place their orders. This predictive capability enables Amazon to position inventory strategically, reducing delivery times and costs.
The automotive industry has embraced automation throughout its supply chain. Toyota's famous just-in-time manufacturing system now incorporates AI-driven demand forecasting and automated replenishment. Parts arrive precisely when needed, reducing storage costs and eliminating waste. Automated quality control systems use computer vision to inspect components with greater accuracy than human inspectors, catching defects that might otherwise reach customers. The result is higher quality, lower costs, and increased production flexibility.
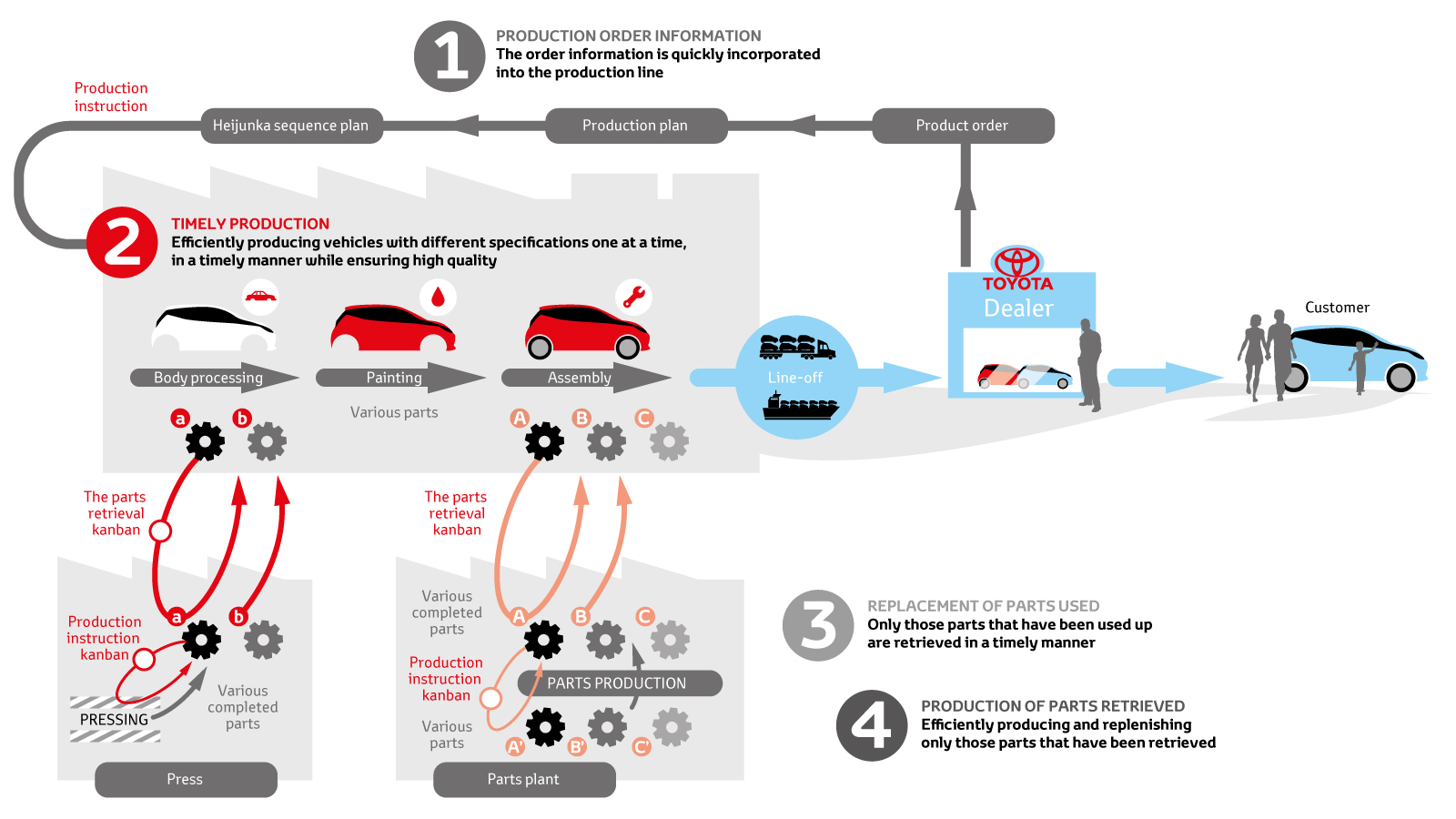
Pharmaceutical supply chains face unique challenges related to product safety, regulatory compliance, and temperature control. Automation addresses these challenges through continuous monitoring and verification. IoT sensors track temperature conditions throughout the cold chain, ensuring that sensitive medications remain within required parameters. Blockchain systems create tamper-proof records of handling and testing, protecting against counterfeiting and enabling precise recalls when necessary. Automated documentation systems ensure regulatory compliance across international boundaries, reducing delays and administrative burdens.
The food and beverage industry has found particular value in automation's ability to ensure safety and freshness. Walmart has implemented blockchain tracking for certain produce items, allowing the company to trace contaminated products to their source in seconds rather than days. Automated temperature monitoring throughout transportation and storage prevents spoilage and extends shelf life. AI-driven demand forecasting reduces waste by ensuring that perishable items are ordered in appropriate quantities based on expected sales.
Even traditional industries like construction are finding value in supply chain automation. Companies like Katerra use digital design tools and automated manufacturing to prefabricate building components with precision, reducing waste and construction time. Automated material tracking systems ensure that components arrive at job sites exactly when needed, eliminating costly delays and storage requirements.
The Business Case for Automation Investment
The decision to invest in supply chain automation requires careful consideration of costs, benefits, and strategic implications. While the initial investment can be substantial, the business case often becomes compelling when viewed through a comprehensive lens.
Cost reduction represents the most immediate and measurable benefit of automation. Labor costs typically account for 50-70% of warehouse operating expenses, making this an obvious target for automation. A single autonomous mobile robot can replace multiple human workers in certain applications, operating continuously without breaks, vacations, or shift changes. Beyond direct labor savings, automation reduces costs associated with errors, waste, and inefficiency. Automated picking systems achieve accuracy rates above 99.9%, virtually eliminating costly mispicks that result in returns and customer dissatisfaction.
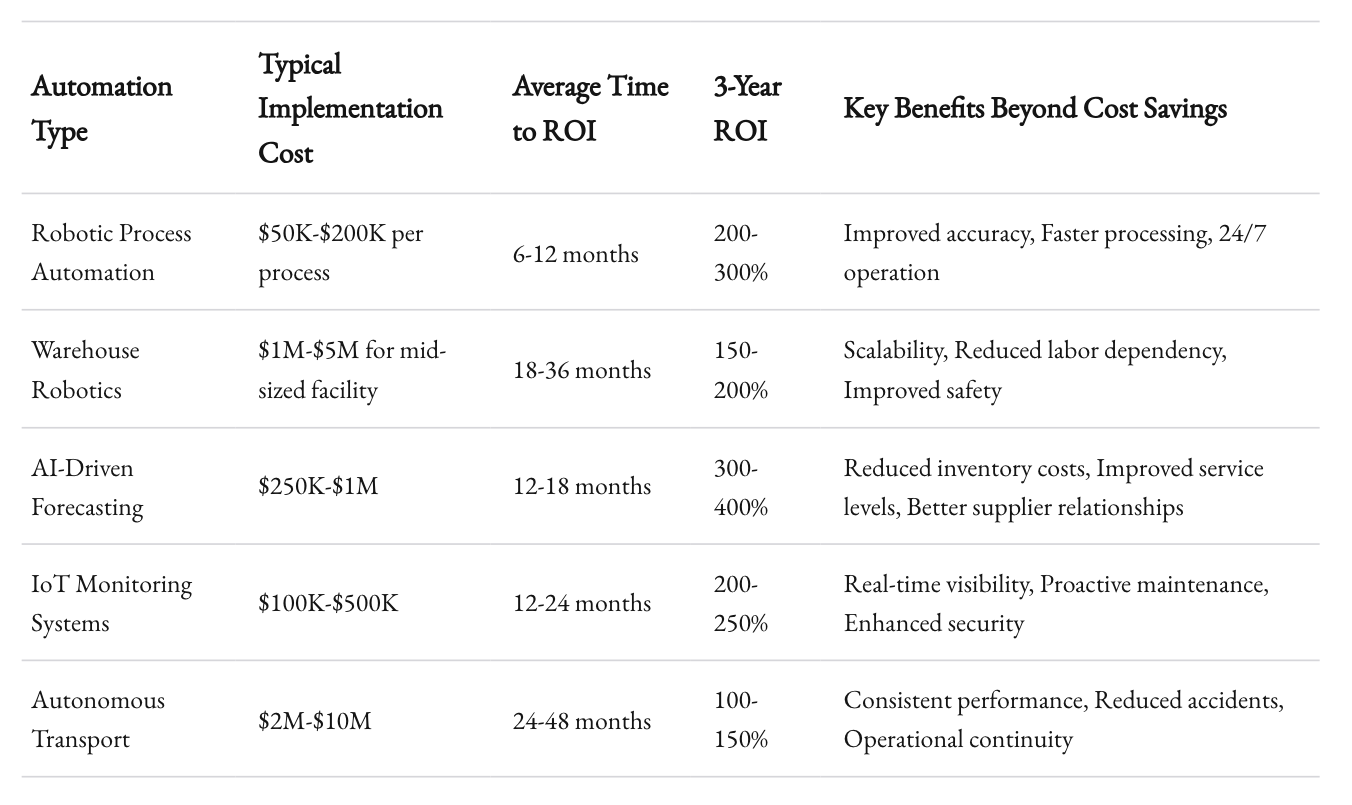
Improved customer experience drives revenue growth and loyalty. In today's market, customers expect fast, accurate fulfillment and real-time visibility into order status. Automation enables companies to meet these expectations consistently. Automated systems can process orders within minutes of receipt, provide accurate delivery estimates based on real-time conditions, and offer customers visibility throughout the fulfillment process. These capabilities translate directly into competitive advantage and customer retention.
Scalability and flexibility represent perhaps the most strategic benefits of automation. Traditional supply chains struggle to handle sudden demand spikes or rapid growth, often requiring months to expand capacity through hiring and training. Automated systems can scale much more quickly, often simply by adding additional robots or expanding software licenses. This scalability enables companies to respond to market opportunities and growth without the constraints of traditional infrastructure.
Risk mitigation has emerged as a critical consideration, particularly following the disruptions of recent years. Automated systems reduce dependence on labor availability in specific locations, enabling operations to continue even during local disruptions. Advanced analytics provide early warning of potential supply chain problems, allowing proactive intervention before disruptions affect customers. Distributed automation capabilities enable companies to shift operations between facilities quickly when necessary, maintaining business continuity through various challenges.
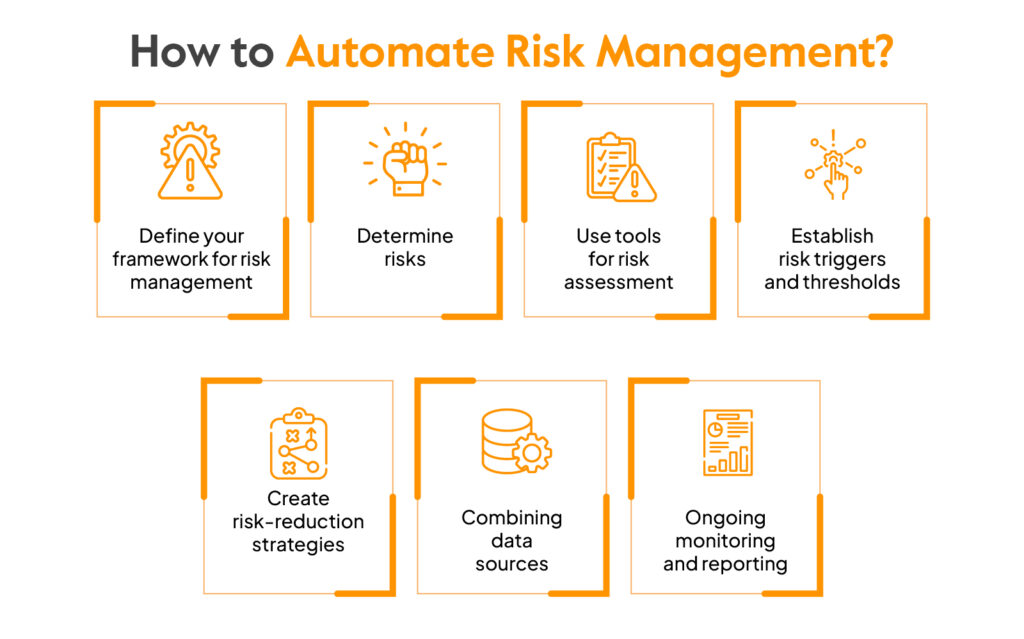
The return on investment timeline varies significantly based on implementation scope and industry context. Simple robotic process automation implementations often achieve ROI within 6-12 months, while comprehensive physical automation systems may require 2-3 years to fully recoup investments. However, companies increasingly recognize that automation is not merely a cost-saving measure but a strategic necessity for remaining competitive in rapidly evolving markets.
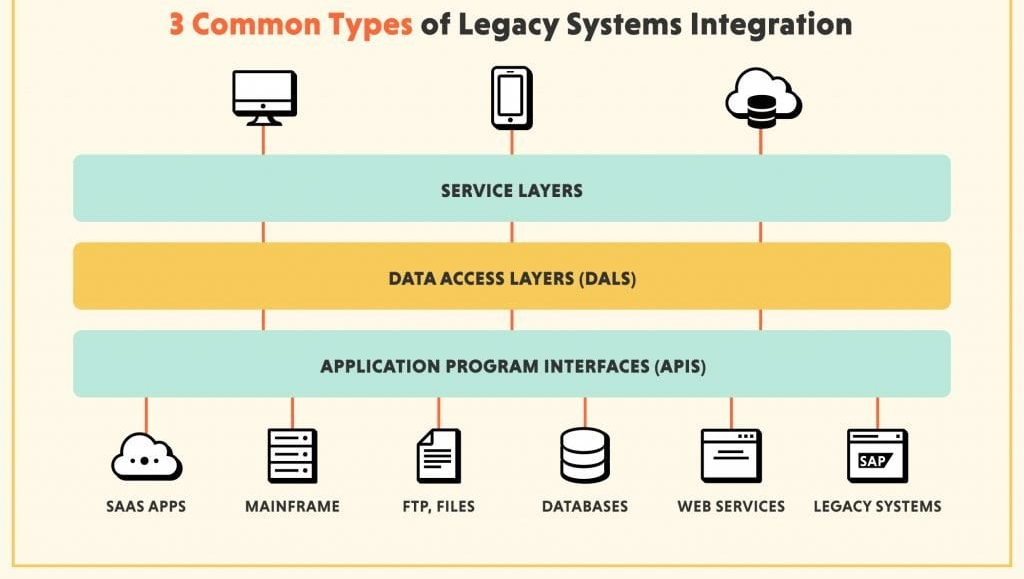
Implementation Challenges and Solutions
Despite compelling benefits, implementing supply chain automation presents significant challenges that must be addressed for successful transformation. Understanding these challenges and proven approaches to overcoming them is essential for companies embarking on automation journeys.
Integration with legacy systems often presents the most immediate technical hurdle. Most established companies operate with a mix of technologies accumulated over decades—from mainframe systems to modern cloud applications. Automation solutions must connect with these diverse systems to access necessary data and execute required actions. Successful companies address this challenge through middleware solutions that create standardized interfaces between systems, API-first architectures that facilitate connections, and phased implementation approaches that gradually replace legacy components without disrupting operations.
Workforce transition requires careful management to avoid disruption and resistance. Automation inevitably changes job requirements and sometimes eliminates certain positions entirely. Forward-thinking companies approach this challenge by involving employees early in the automation process, identifying opportunities for workers to move into higher-value roles, and investing in training programs that equip employees with skills needed to work alongside automated systems. Companies like Schneider Electric have created internal "automation academies" that retrain workers for new roles supervising and maintaining automated systems.
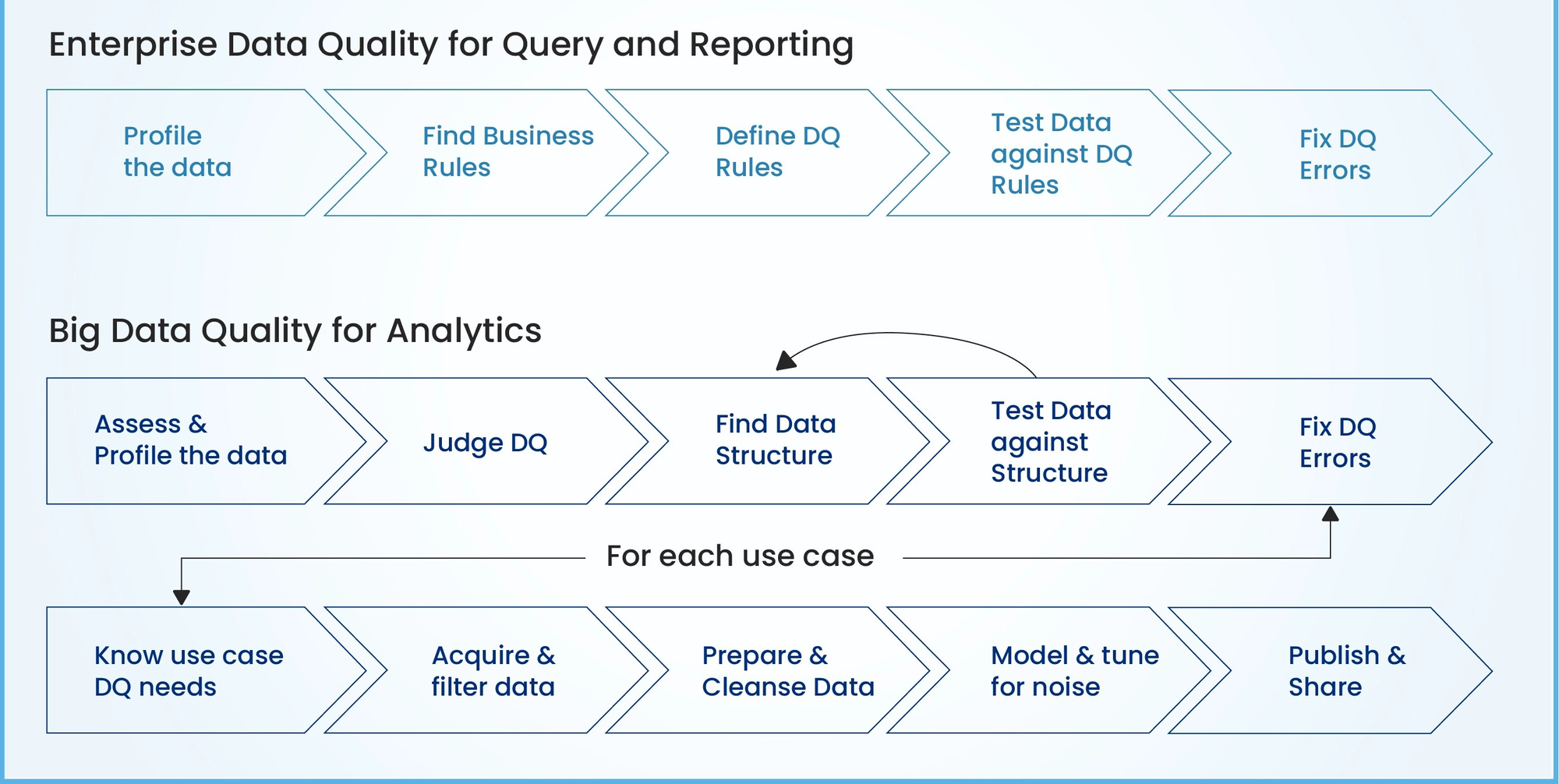
Data quality and governance become increasingly critical as automation systems rely on accurate information to make decisions. Poor data quality can lead automated systems to make incorrect decisions at scale—a problem that compounds quickly. Successful implementations include robust data governance frameworks that establish standards, ownership, and processes for maintaining data integrity. Many companies create dedicated data quality teams responsible for monitoring and improving the information that feeds automated systems.
Security concerns intensify as supply chains become more connected and automated. Each connected device, sensor, or system represents a potential entry point for cyber threats. Addressing these concerns requires comprehensive security architectures that include encryption, access controls, regular security audits, and incident response plans. Leading companies adopt "security by design" approaches that incorporate protection measures from the earliest stages of automation implementation rather than adding them as afterthoughts.
Change management ultimately determines whether automation delivers its potential value. Even the most sophisticated technology fails without effective organizational adoption. Successful implementations include clear communication about automation objectives, executive sponsorship that demonstrates commitment, performance metrics that align with automation goals, and celebration of early wins that build momentum. Companies like Procter & Gamble have created dedicated transformation offices that coordinate automation initiatives across functions and geographies, ensuring consistent approaches and shared learning.
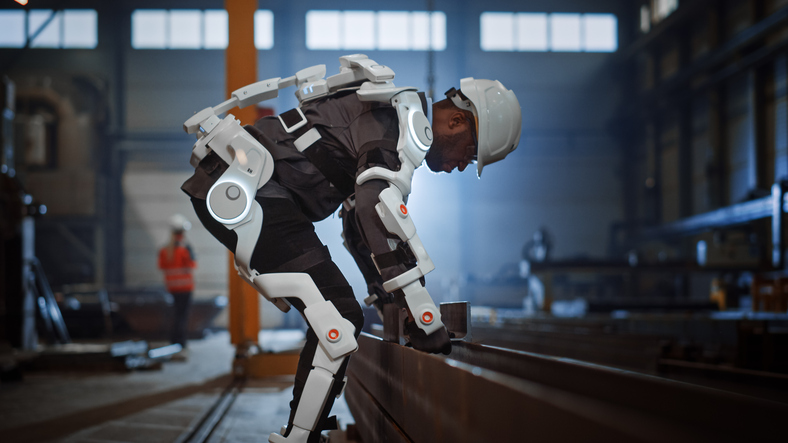
The Human Element in Automated Supply Chains
Despite the focus on technology, successful supply chain automation ultimately depends on human factors. The relationship between people and automated systems determines whether companies realize the full potential of their investments.
The changing nature of work represents both a challenge and an opportunity. Automation eliminates certain tasks—particularly those that are repetitive, dangerous, or require minimal judgment. However, it simultaneously creates demand for new skills and roles. Warehouse associates who once spent their days picking items now supervise fleets of robots, intervening when unusual situations arise. Supply chain analysts who previously compiled basic reports now focus on interpreting AI-generated insights and making strategic recommendations. These evolved roles typically offer higher satisfaction and compensation while requiring different capabilities.
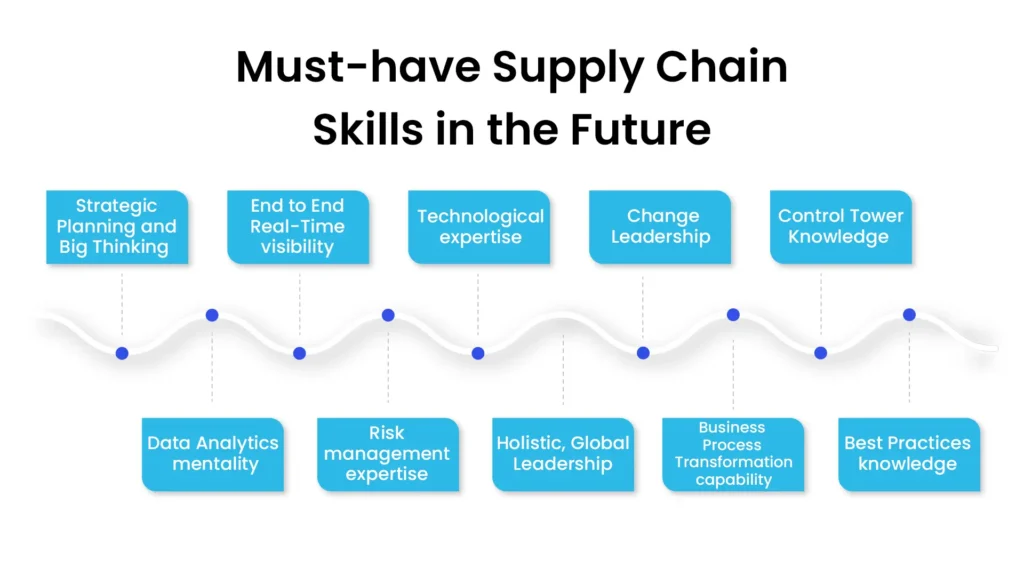
Skill development becomes a strategic priority in automated environments. Companies must invest in training programs that prepare workers for collaboration with automated systems. These programs include technical training on specific platforms and technologies, but also emphasize uniquely human capabilities that complement automation—critical thinking, creative problem-solving, interpersonal communication, and adaptability. Organizations like DHL have created immersive training environments where workers practice interacting with automated systems before encountering them in production environments.
Leadership approaches must evolve to effectively manage automated operations. Traditional command-and-control management styles become less relevant as automated systems handle routine execution. Instead, leaders must focus on setting direction, removing obstacles, fostering innovation, and developing talent. They must understand technology sufficiently to make informed decisions without necessarily possessing deep technical expertise. Companies like Unilever have created specialized leadership development programs focused on digital transformation and human-machine collaboration.
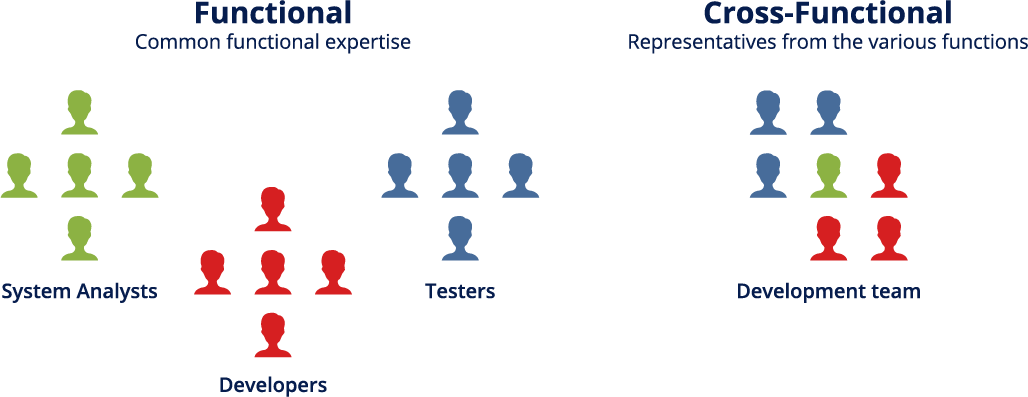
Organizational structures typically flatten as automation reduces the need for multiple management layers focused on supervision and coordination. Cross-functional teams become more common, bringing together technical specialists, operations experts, and business analysts to address complex challenges. Decision-making often becomes more distributed, with frontline teams empowered to make adjustments within parameters established by automated systems.
The most successful organizations view automation not as a replacement for human workers but as an augmentation of human capabilities. They identify tasks best suited to automation—those requiring precision, consistency, speed, and handling of large data volumes—while preserving human involvement in areas requiring judgment, creativity, emotional intelligence, and ethical consideration. This balanced approach maximizes the strengths of both humans and machines while creating more engaging work environments.

Future Trends and Emerging Technologies
The supply chain automation landscape continues to evolve rapidly, with several emerging technologies and trends poised to drive the next wave of transformation. Understanding these developments helps companies prepare for future opportunities and challenges.
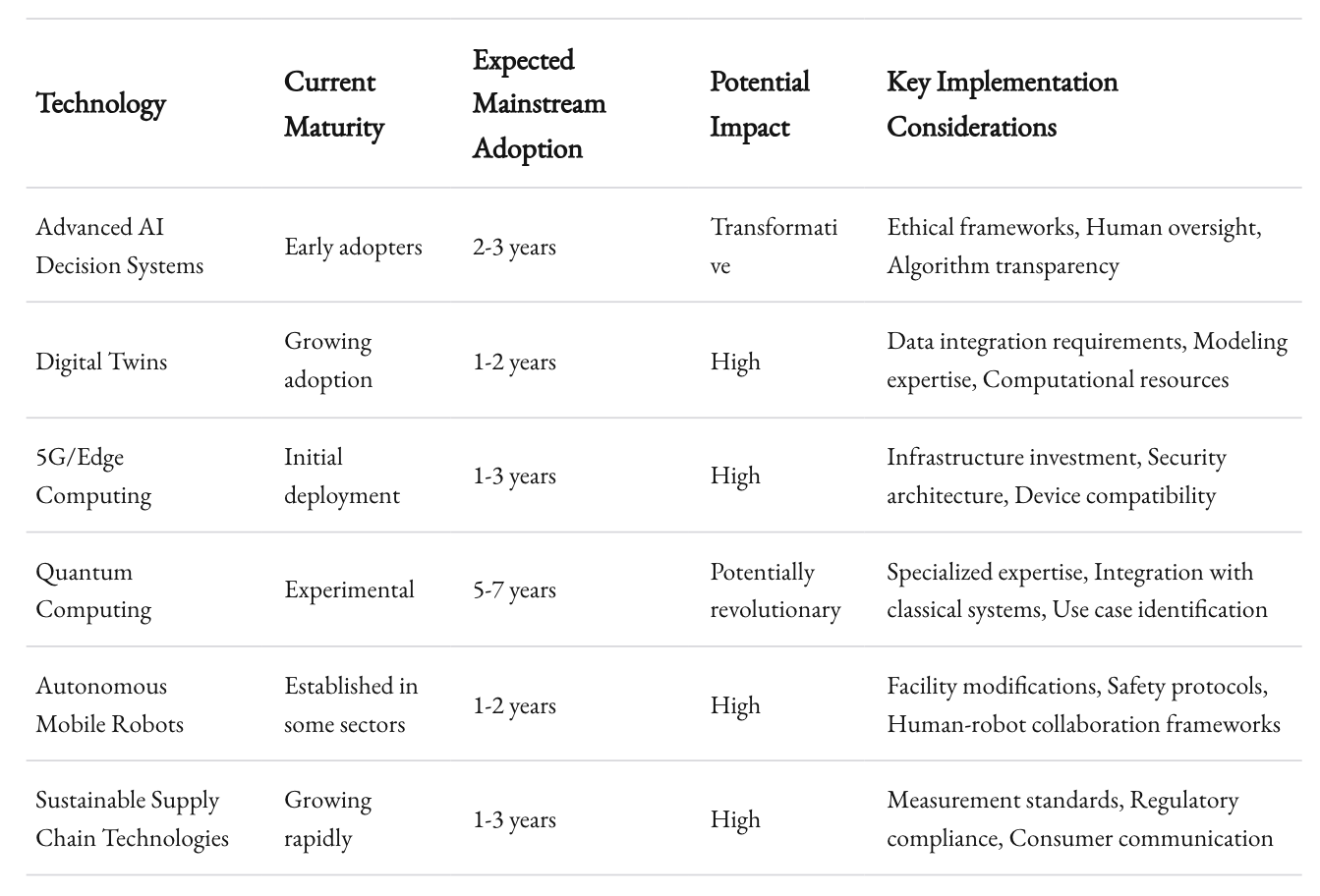
Artificial Intelligence is advancing beyond basic prediction and optimization toward more autonomous decision-making. Next-generation AI systems will increasingly make complex decisions without human intervention, adjusting supply chain parameters in real-time based on changing conditions. For example, AI might automatically reroute shipments around weather disruptions, adjust production schedules based on emerging demand patterns, or negotiate with suppliers' systems to secure additional materials when needed. These capabilities will enable supply chains to respond to changes with unprecedented speed and precision.

Digital twins represent virtual replicas of physical supply chains, enabling simulation and optimization before implementation in the real world. These sophisticated models incorporate real-time data from IoT sensors, historical performance information, and external factors like weather and traffic. Companies use digital twins to test scenarios, identify potential problems, and optimize operations without disrupting actual processes. As computing power increases and modeling techniques improve, digital twins will become increasingly accurate and valuable for continuous optimization.
5G and edge computing are transforming how supply chain data is collected, processed, and utilized. The high bandwidth and low latency of 5G networks enable real-time communication between countless devices, while edge computing allows processing to occur closer to data sources rather than in centralized data centers. Together, these technologies enable applications like autonomous vehicles in yards and warehouses, real-time quality inspection using computer vision, and instantaneous decision-making at remote locations. Companies like Maersk are already implementing private 5G networks at port facilities to enable advanced automation applications.
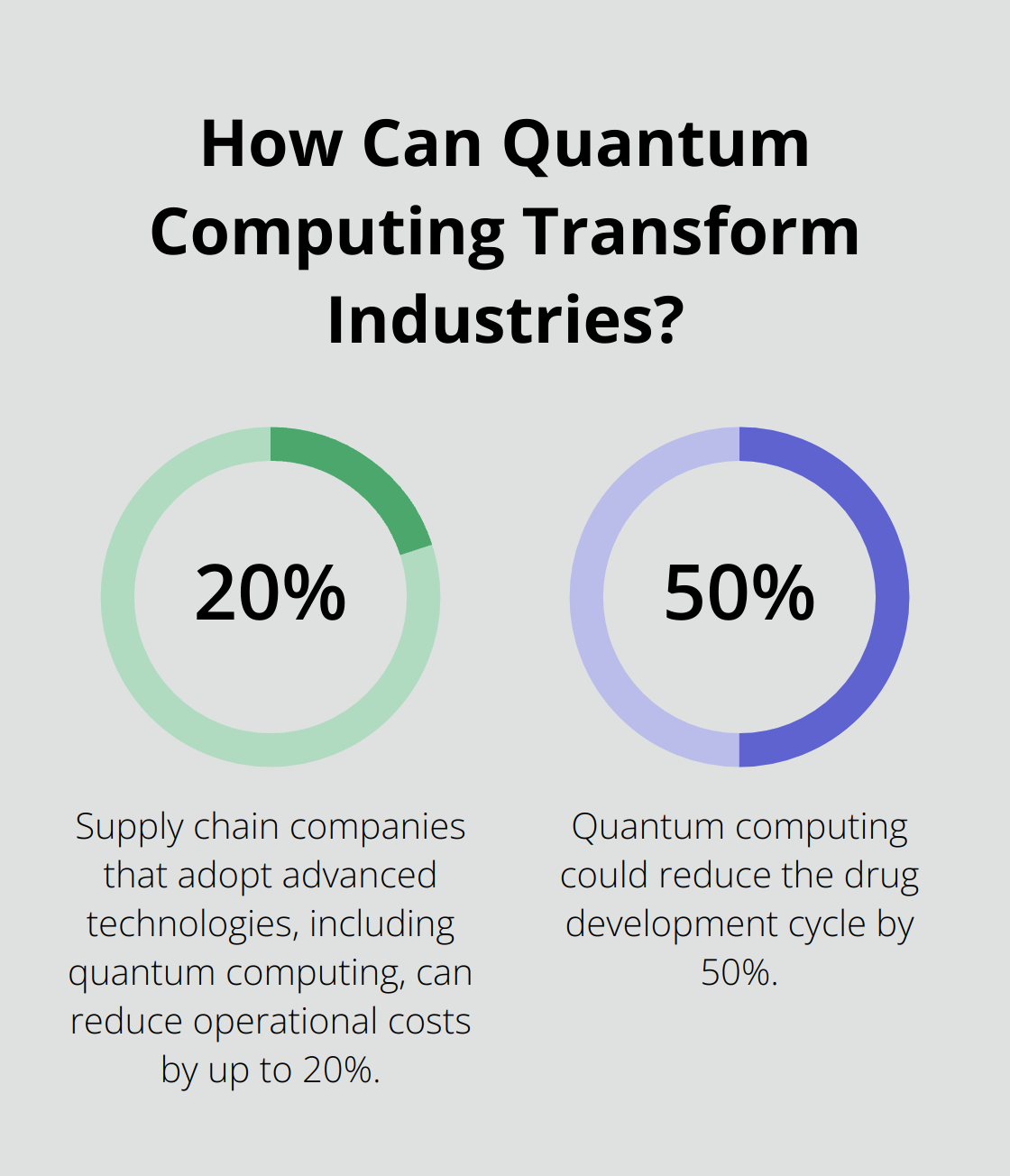
Quantum computing, while still emerging, holds particular promise for supply chain optimization problems that overwhelm traditional computing approaches. Complex routing, scheduling, and allocation problems that currently require simplification or approximation could potentially be solved optimally using quantum approaches. While practical applications remain several years away, leading companies are already exploring quantum algorithms for supply chain optimization and forming partnerships with quantum computing providers to prepare for this technological leap.
Sustainability requirements are increasingly shaping automation strategies as companies face pressure to reduce environmental impacts. Future automation systems will optimize not just for cost and speed but also for carbon footprint, waste reduction, and resource efficiency. AI systems will calculate environmental trade-offs alongside financial considerations, helping companies balance competing objectives. Automated systems will increasingly incorporate circular economy principles, facilitating product returns, remanufacturing, and recycling as integral parts of supply chain operations.
Developing a Strategic Automation Roadmap
Implementing supply chain automation requires a structured approach that aligns technology investments with business objectives and organizational capabilities. A well-designed roadmap guides companies through the transformation journey while maximizing return on investment.
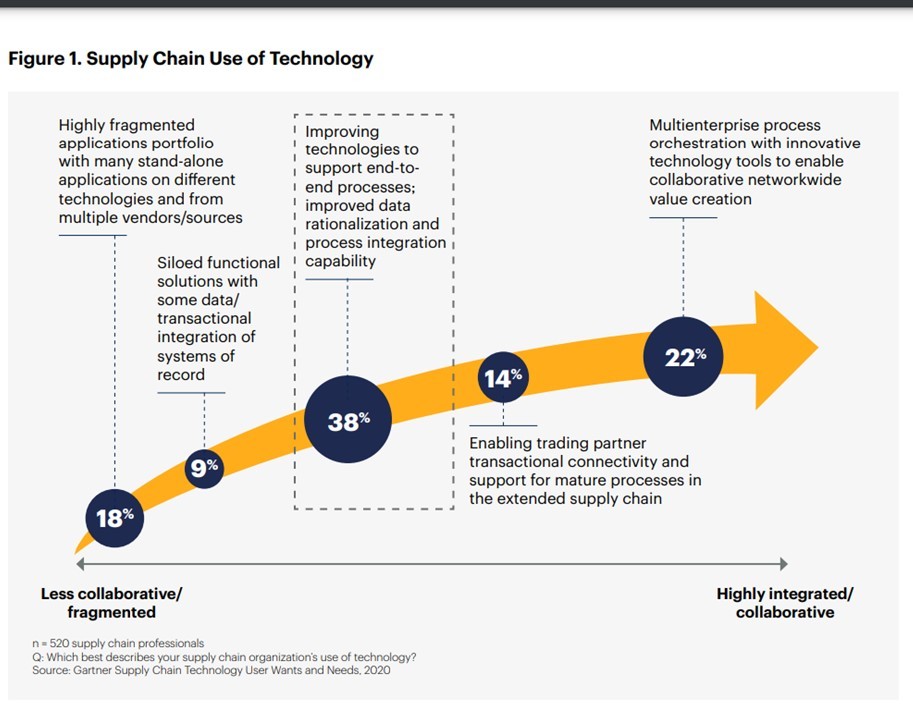
Assessment and prioritization form the essential first step. Companies must evaluate their current supply chain operations, identifying pain points, inefficiencies, and opportunities for improvement. This assessment should consider quantitative metrics like cost, cycle time, and error rates alongside qualitative factors like customer satisfaction and employee experience. The most successful approaches involve cross-functional teams that bring diverse perspectives to the evaluation process. From this assessment, companies can prioritize automation opportunities based on potential impact, implementation complexity, and strategic alignment.
Technology selection requires careful consideration of both current needs and future flexibility. Companies must evaluate vendor solutions against specific requirements while considering factors like integration capabilities, scalability, security, and support. The technology landscape continues to evolve rapidly, making flexibility and adaptability critical considerations. Leading companies often create proof-of-concept implementations to test solutions in real-world environments before committing to full-scale deployment. They also consider build-versus-buy decisions carefully, recognizing that custom development may be appropriate for capabilities that provide unique competitive advantage.
Implementation approaches vary based on organizational context and risk tolerance. Some companies prefer comprehensive transformation programs that implement automation across multiple functions simultaneously, while others adopt more incremental approaches focused on specific processes or locations. The comprehensive approach offers faster results but involves higher risk and change management challenges. The incremental approach provides learning opportunities and builds momentum through early wins but may sacrifice some integration benefits. Regardless of approach, successful implementations include clear milestones, defined success metrics, and regular progress reviews.
Governance structures ensure that automation initiatives remain aligned with business objectives and deliver expected benefits. Effective governance includes executive sponsorship, clear decision-making processes, and regular review mechanisms. Many companies establish automation centers of excellence that maintain standards, share best practices, and provide specialized expertise across the organization. These centers typically include both technical specialists and business process experts who collaborate to ensure that automation solutions address real business needs rather than implementing technology for its own sake.
Continuous improvement mechanisms recognize that automation is not a one-time project but an ongoing journey. Leading companies establish feedback loops that capture performance data, user experiences, and emerging challenges. They create regular review cycles to evaluate automation effectiveness and identify opportunities for enhancement. They also maintain connections with technology providers, research organizations, and industry groups to stay informed about emerging capabilities and best practices.
Case Study: 1985's Approach to Supply Chain Automation
As an outsourced software development company, 1985 has helped numerous clients transform their supply chains through strategic automation. Their approach combines technical expertise with deep business understanding, enabling solutions that deliver measurable value.
One of 1985's clients, a mid-sized consumer packaged goods manufacturer, faced increasing pressure from retail customers for faster fulfillment and greater visibility. Their legacy systems couldn't keep pace with growing demands, resulting in missed delivery windows and strained customer relationships. The company engaged 1985 to develop an automation strategy that would address these challenges while working within budget constraints.
1985 began with a comprehensive assessment of the client's existing processes, systems, and pain points. They conducted workshops with stakeholders from across the organization, analyzed performance data, and benchmarked operations against industry standards. This assessment revealed several key opportunities: order processing delays caused by manual data entry, inventory inaccuracies resulting from batch updates, and limited visibility into shipment status once products left the warehouse.
Based on this assessment, 1985 developed a phased automation roadmap that prioritized high-impact, lower-complexity initiatives for early implementation. The first phase focused on robotic process automation for order processing, eliminating manual data entry and reducing processing time from hours to minutes. The second phase implemented real-time inventory management with IoT sensors on key storage locations, improving accuracy from 92% to 99.5%. The third phase added predictive analytics for demand forecasting, reducing both stockouts and excess inventory.
Throughout implementation, 1985 emphasized knowledge transfer and capability building. They worked closely with the client's IT team, providing training and documentation that enabled internal resources to maintain and enhance the automated systems. They also helped establish a continuous improvement process that regularly evaluated automation performance and identified opportunities for refinement.
The results proved transformative. Order processing costs decreased by 62%. Perfect order fulfillment rates increased from 85% to 97%. Inventory carrying costs decreased by 23% while product availability improved. Perhaps most importantly, the company's Net Promoter Score from retail customers increased significantly, strengthening key relationships and enabling business growth.
This case exemplifies 1985's approach to supply chain automation: start with business objectives, prioritize based on impact and feasibility, implement incrementally, build internal capabilities, and measure results rigorously. This methodology has proven effective across industries and company sizes, delivering consistent value while managing implementation risks.

The Imperative for Action
Supply chain automation has transitioned from competitive advantage to competitive necessity. Companies that delay implementation risk falling behind competitors who leverage automation to deliver better customer experiences at lower costs with greater resilience. The gap between leaders and laggards widens daily as automated systems continuously improve through machine learning and accumulated data.
The COVID-19 pandemic accelerated this transition, exposing vulnerabilities in traditional supply chains while highlighting the resilience of automated operations. Companies with advanced automation capabilities adapted more quickly to disruption, maintained higher service levels during uncertainty, and recovered faster as conditions stabilized. This real-world stress test convinced many executives that automation investments deliver not just efficiency but essential business continuity capabilities.
For companies beginning their automation journey, several principles can guide successful implementation:
Start with clear business objectives rather than technology for its own sake. The most successful automation initiatives address specific pain points or opportunities with measurable value.
Prioritize based on impact, feasibility, and strategic alignment. Not all processes should be automated simultaneously—focus first on high-value, lower-complexity opportunities that build momentum.
Invest in people alongside technology. Automation changes how people work but rarely eliminates the need for human involvement. Training, change management, and organizational redesign are essential components of successful automation.
Maintain flexibility for future evolution. The technology landscape continues to change rapidly, making adaptability a critical consideration in architecture and vendor decisions.
Measure and communicate results consistently. Quantifying automation benefits builds support for continued investment while identifying opportunities for refinement.
The supply chain of tomorrow will bear little resemblance to traditional models. It will be more connected, more intelligent, more responsive, and more resilient. It will anticipate problems before they occur, adapt to changing conditions in real-time, and continuously optimize based on accumulated learning. Most importantly, it will enable companies to deliver products and services with unprecedented speed, accuracy, and efficiency.
The question for business leaders is not whether to automate but how quickly and comprehensively to embrace this transformation. Those who move decisively now position themselves for competitive advantage in an increasingly digital marketplace. Those who wait may find the gap increasingly difficult to close as automated supply chains continue their rapid evolution.
The revolution is here. The time for action is now.